The single most important thing right now for US and Mexico Plant Managers is the safety and wellbeing of their employees, and the ability to keep their facilities operational. For weeks, most non-essential plants have been closed, and the mere risk of a shutdown has most plants closing their doors completely to visitors, instituting advanced cleaning procedures, and implementing new technology solutions to track employees and potential issues in real-time, all while they attempt to reopen and stay open.
When it comes to quality, there are several potential issues to deal with that can have an impact, including:
- Insufficient personnel with insufficient training and high rotation.
- Fewer quality checks and reduced access to outside resources due to a no visitors policy.
- The future risk of having to restart operations after a shutdown.
All three of these situations can significantly increase the risk of a quality disruption, which can exacerbate the problem if you don’t already have a quality containment solution in-house.
Offsite Containment Solutions
One of the ways you can stay ahead of these potential issues is through offsite containment. By leveraging a partner organization with an offsite facility, you can source your containment needs without introducing new risk to your facility.
Through proactive containment, you can:
- Evaluate the effectiveness of each of your existing quality protection layers.
- Create new layers beyond initial visual inspections - these are often not 100% effective, so having a secondary layer to protect is important.
- Determine if the gauges and tools you have are sufficient for a comprehensive inspection.
When downtime and quality disruption can potentially cost your organization millions, protecting quality becomes more important than ever.
Five Front Line Challenges and How to Address Them
Making the situation more difficult is the fact that many plants are facing new challenges in how to manage their workers, reduce exposure, and quickly identify risk. We’ve collected some of the most common front line challenges and how organizations are addressing them with quality in mind.
- Responding to a Verified Coronavirus Case - If an employee tests positive, it’s imperative that you have a system in place to accurately identify everyone they have been in contact with, the locations that need to be quarantined and cleaned, and a tracking system to ensure they get proper care and return only after full recovery and quarantine. Traceability through geolocation and time stamp can help with this.
- Front Line Workers Lack Email Addresses - Communication is made even more difficult by the lack of a single, centralized communication channel. Bring your own device policies combined with Digital Andon Cord software can help address this, connecting all front line workers and supervisors.
- Regular Disinfection and Cleaning Needs - Your facilities need to be cleaned carefully and regularly, and that needs to be tracked. Combined with existing quality challenges, it’s a big ask with a smaller staff. Digital checklists can help to ensure nothing is missed and all cleanings are properly validated and verified.
- Limited Access to Overseas Resources - If you have overseas support staff for equipment maintenance, machine controls, process audits or compliance audits, they very well may not be able to visit your plant due to closed borders. Remote guidance will be needed to ensure equipment and processes are evaluated correctly without interruption.
- Quarantine of Vital Management Staff - Remote access to key resources, digital communications tools, and Andon Cord technology are vital to keep managers and supervisors in touch with their teams, even if they have been quarantined at home due to an infection or exposure.
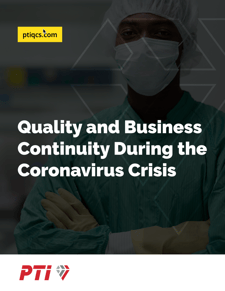
The bottom line is that technology matters. PTI QCS has invested carefully to build a digital foundation that supports our quality containment efforts. Through the use of Safely Pass, we’ve connected our front line workers to ensure the best quality of communication across all of our organizations.
Download our eBook, Quality and Business Continuity During the Coronavirus Crisis, to learn about our recommended approach to quality containment and business continuity during the current crisis.